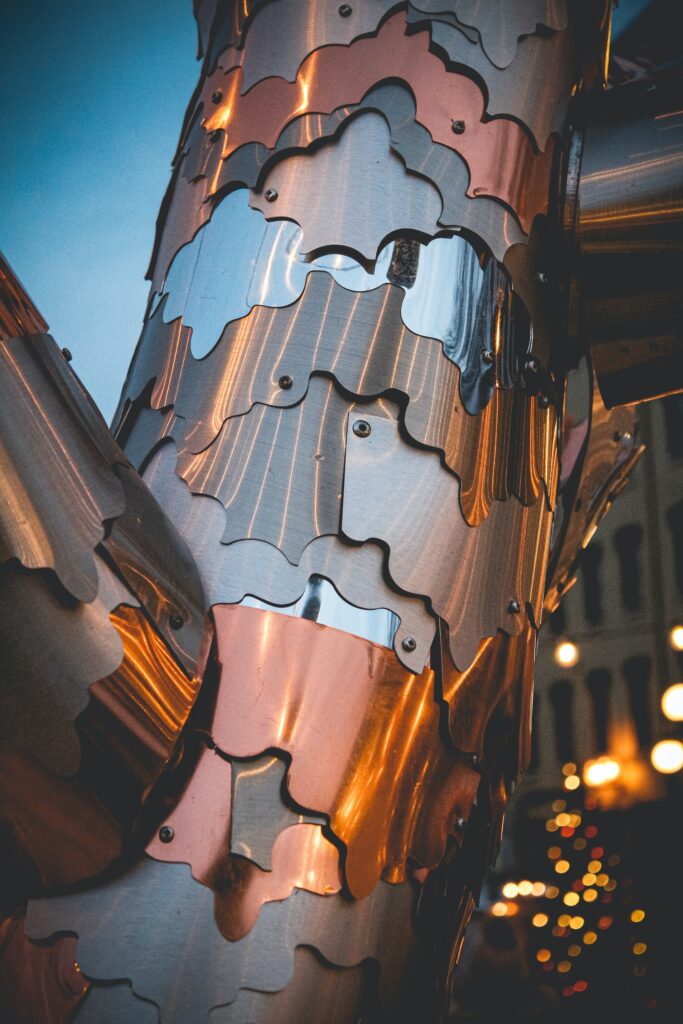
In the world of modern manufacturing and fabrication, precision and efficiency are paramount. Laser cutting sheet metal has emerged as a revolutionary technology that has redefined the industry’s landscape. With the ability to cut intricate shapes, fine details, and complex patterns, laser cutting offers unparalleled accuracy and repeatability. In this article, we will delve into the world of laser cutting sheet metal, exploring its principles, applications, advantages, and the transformative impact it has had on the manufacturing and design industries.
The Principles of Laser Cutting
- The Laser Source: Laser cutting utilizes a high-energy laser beam that is focused onto a small spot. The source of this laser can be a carbon dioxide (CO2) laser, neodymium-doped yttrium aluminum garnet (Nd:YAG) laser, or fiber laser.
- Material Interaction: When the laser beam contacts the surface of the metal sheet, it rapidly heats the material to its melting or vaporization point. The focused energy creates a narrow, high-temperature zone called the kerf.
- Assist Gas: An assist gas, typically oxygen or nitrogen, is used to blow away the molten or vaporized material, leaving a precise cut. The choice of assist gas depends on the material being cut and the desired finish.
- Computer Numerical Control (CNC): Laser cutting machines are equipped with CNC systems that precisely control the movement of the laser beam. This allows for the accurate execution of programmed designs.
Applications of Laser Cutting
Laser cutting is a versatile technology that finds applications in various industries, including but not limited to:
- Automotive: Laser cutting is used for precision cutting of vehicle body panels, chassis components, and intricate parts. The technology allows for tight tolerances and high repeatability in automotive manufacturing.
- Aerospace: The aerospace industry benefits from laser cutting for the production of lightweight components, such as aircraft skins and engine parts. The precision and quality of laser-cut parts are essential in aerospace engineering.
- Architecture and Design: Architects and designers use laser cutting to create intricate decorative elements, facades, and building components. It allows for the realization of complex designs and patterns.
- Electronics: In the electronics industry, laser cutting is employed for precise cutting of circuit boards, components, and enclosures. The technology enables intricate, small-scale designs and prototypes.
- Medical Devices: Laser cutting is crucial in the production of medical devices and instruments. It ensures precision and cleanliness in the fabrication of items like stents, catheters, and surgical tools.
- Art and Fashion: Artists and fashion designers use laser cutting to craft intricate patterns in fabrics, leather, and other materials. The technology allows for the creation of detailed and customized designs.
- Metal Fabrication: In general metal fabrication, laser cutting is used for diverse applications, from custom signage and architectural elements to machinery components and enclosures.
Advantages of Laser Cutting
- Precision: Laser cutting offers unmatched precision and accuracy. The focused laser beam can cut intricate shapes, sharp corners, and fine details with minimal distortion.
- Repeatability: Laser cutting machines are highly reliable and can reproduce the same cut repeatedly without variations, making it ideal for mass production.
- Versatility: Laser cutting is suitable for a wide range of materials, including metals (steel, aluminum, stainless steel), plastics, ceramics, and even composites.
- Reduced Material Waste: The narrow kerf width and minimal heat-affected zone of laser cutting result in less material wastage, making it a sustainable choice.
- Minimal Post-Processing: Laser-cut parts often require minimal or no post-processing, reducing production time and costs.
- Fast Cutting Speed: Laser cutting is a high-speed process, enabling quick turnaround times for manufacturing and prototyping.
- Complex Geometries: The ability to cut intricate and complex geometries opens up new design possibilities for engineers, architects, and designers.
Laser Cutting Techniques
- CO2 Laser Cutting: CO2 lasers are commonly used for cutting non-metal materials, such as wood, acrylic, and plastics. They are efficient at vaporizing organic materials and offer a clean cut.
- Fiber Laser Cutting: Fiber lasers are renowned for their exceptional precision and speed when cutting thin to thick metals. They are well-suited for applications like stainless steel and aluminum cutting.
- N2 and O2 Cutting: The choice of assist gas, nitrogen (N2) or oxygen (O2), influences the laser cutting process. Nitrogen is often used for clean, oxide-free cuts on stainless steel and aluminum, while oxygen provides a faster cut for carbon steel.
- Dual- or Multi-Mode Laser Cutting: Dual-mode lasers can switch between higher and lower-power modes, allowing for greater flexibility in cutting different materials. Multi-mode lasers provide even more versatility in adjusting power levels for various applications.
Challenges and Considerations
- Material Thickness: While laser cutting is highly versatile, its effectiveness may diminish for extremely thick materials, which may require other cutting methods like plasma or waterjet cutting.
- Reflective Materials: Highly reflective materials like copper and brass can be challenging to cut with conventional laser systems. Specialized systems are required for cutting these materials.
- Energy Consumption: Laser cutting equipment consumes a significant amount of energy, and the operation of powerful lasers can be costly in terms of electricity.
- Initial Investment: The purchase and installation of laser cutting machines represent a significant upfront investment. Smaller businesses may face barriers to entry due to these costs.
Future Developments in Laser Cutting
- Hybrid Laser Cutting: Combining laser technology with other cutting methods, such as waterjet or plasma cutting, offers new possibilities for improved cutting quality and reduced operating costs.
- 3D Laser Cutting: Advancements in 3D laser cutting technology enable the fabrication of complex 3D components and assemblies, expanding the applications of laser cutting.
- Laser Automation: The integration of automation, including robotic arms and material handling systems, is becoming more common to enhance efficiency and reduce labor costs.
- Additive Manufacturing and Laser Cutting Integration: Combining laser cutting with additive manufacturing techniques allows for the production of highly complex and customized parts with precision.
Laser cutting sheet metal is a transformative technology that has left an indelible mark on modern manufacturing and design. Its precision, versatility, and efficiency have enabled the creation of intricate components, artistic designs, and functional structures. As the technology continues to evolve and adapt to emerging challenges and materials, the future of laser cutting holds promise for even greater advancements in various industries, from aerospace to fashion, making it a vital component of the manufacturing landscape.